A industria automotiva está em constante processo de evolução para atender uma demanda de mercado cada vez mais globalizada e exigente. Suas estratégias estão em constantes revisão para alcançar metas, estabelecer novas parcerias e se diferenciar em mercados emergentes.
Com foco em melhoria continua, redução de custos, processos mais eficientes e, mais recentemente, satisfação do cliente a rastreabilidade industrial é uma ferramenta fundamental para alcançar todos estes resultados.
A rastreabilidade na industria automotiva é um processo que documenta, desde a sua origem, componentes e sub-montagens as associando com um veículo especifico ou com uma família de veículos. As informações mais comuns nesta documentação podem variar, mas as mais utilizadas são:
- Fornecedor
- Planta onde foi produzida
- Origem (cidade, país)
- Data e hora da montagem
- Número de lote
- Código do produto
- Modelo
- Número de série
- Data de validade
Esta informação pode ser compilada e gravada em um único código de barras a ser gravado no componente (DMP – Direct Part Marking) e este código pode ser decodificado durante o processo produtivo por leitores e câmeras e a informação disponibilizada com segurança para o sistema de gerenciamento da planta (ERP ou MES), assegurando a rastreabilidade completa dos componentes de cada veículo produzido.
OS OBJETIVOS DE UM PROGRAMA DE RASTREABILIDADE
A identificação dos produtos é vital para aqueles fabricam, armazenam e transportam componentes ao longo da cadeia produtiva, pois esta informação é utilizada para cálculos de desempenho, estoque, previsões, garantia, reparos e pós-venda que são fundamentais para tomadas de decisão para redução de custo e aumento da eficiência.
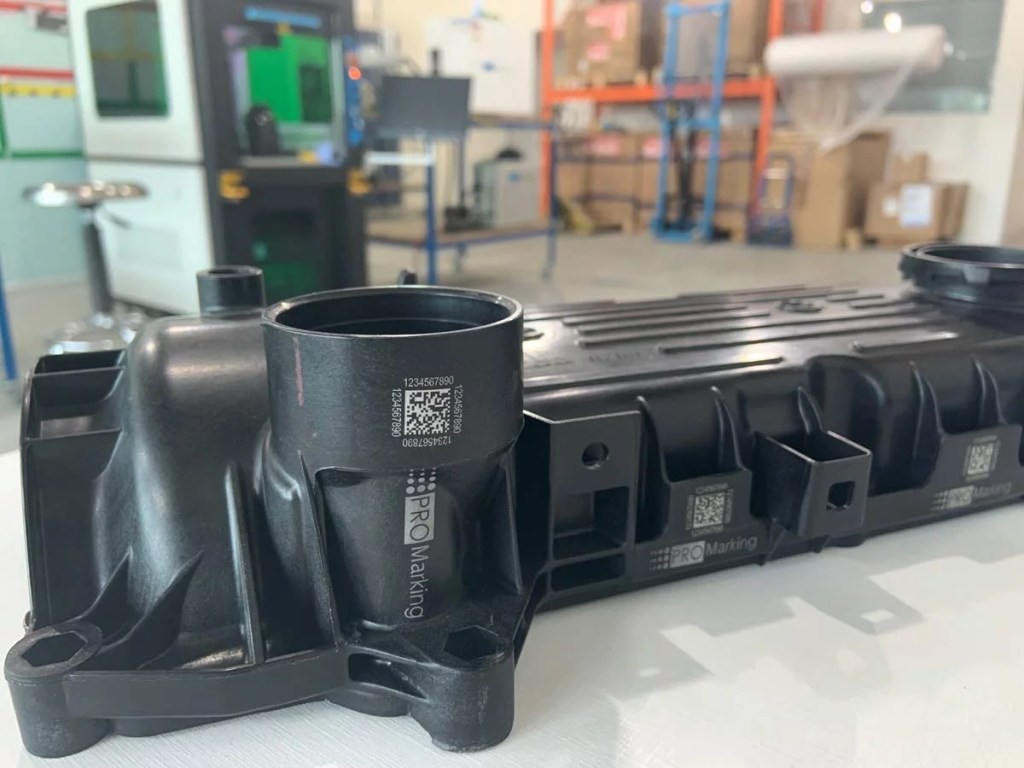
Monitoramento do Processo de Controle
Sistemas de rastreabilidade em tempo real podem ajudar na redução do tempo de entrega dos produtos dentro da cadeia produtiva gerando informações individuais sobre cada estação de trabalho. Estes sistemas são baseados em marcos do material em processamento (WIP) associados a dados de outros sistemas de gerenciamento. Se ou quando for encontrado um gargalo será fácil identificar onde e qual o problema.
Implementação de métodos a prova de erros
Poka Yoke (um método a prova de erros utilizado no processo de Manufatura LEAN) aumenta a qualidade assegurando que os processos sejam realizados na sequência correta, da maneira adequado e utilizado as peças certas. Além de eliminar os problemas causados pela entrada manual de informações incorretas, o sistema baseado na leitura de códigos de barras também pode auxiliar com informações para segurança, garantia e atender especificações das agências regulatórias.
Redução de desperdícios e Recalls
Lidar com um problema de qualidade de componente dentro da Automobilística, usualmente chamado de “scrap”, pode custar em R$ 100 mil e R$ 2 mi. Este valor mostra quanto custa para encontrar um componente defeituosos, conserta-lo e para encontrar e consertar conjuntos comprometidos pelo problema de qualidade do primeiro componente. Se o componente já estiver dentro da montadora, então os custos de reparo podem subir exponencialmente (a partir de R$ 4 mi), além de impactar negativamente na imagem do fornecedor junto à montadora. Caso o componente defeituoso chegue até o cliente final, o custo de um recall pode custar 10 vezes este valor. Com um programa de rastreabilidade consistente, estes custos permaneceram baixos e sem transtorno à imagem da empresa junto ao seu cliente e consumidor final.
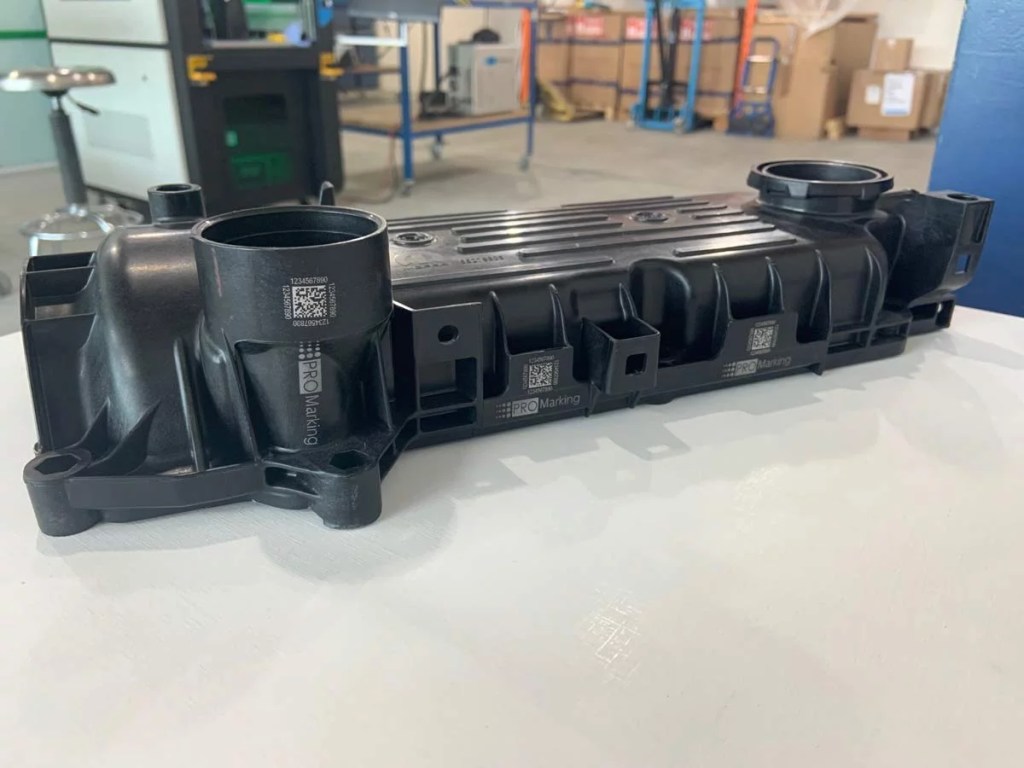
LAYOUT COM CICLO COMPLETO DE PRODUÇÃO
Componentes Primários_ Número de Série e outras informações como data, hora, localização, número de desenho e fornecedor podem ser convertidos em códigos de barras gravados na superfície dos componentes.
Códigos de barras podem incluir instruções de armazenamento. Em uma linha com alto índice de automação, onde robôs são responsáveis pela separação e destinação de componentes, os códigos de barras podem ser lidos por leitores fixos espalhados pela linha e assim instruções sobre a destinação serão repassadas em tempo real para todos os periféricos. Desta maneira, é possível assegurar que o componente correto estará disponível na hora certa e no local adequado.
Localização WIP (Material em processamento)_ Os processos subsequentes à gravação e também o ambiente podem deteriorar a qualidade do código gravado e portanto, é importante garantir uma boa qualidade de gravação para que o código possa ser lido durante toda a sua jornada na cadeia produtiva. As gravadoras à laser da linha Prolase são capazes de gravar materiais rugosos, garantindo sua qualidade durante toda o processo.
Submontagem_ Um histórico da produção pode ser criado a partir da leitura de códigos de barras e os integrando dentro de um ERP. Para evitar erros, grande parte dos fabricantes gera fichas de produção para auxiliar o processo de montagem de subconjuntos. Este procedimento ajuda os operadores a evitar erros de montagem em aplicações com muitos componentes similares. O resultado é o aumento da produtividade e da qualidade com redução de descarte e retrabalho. Além do que, o monitoramento do processo garante que todas as etapas foram cumpridas e todos os componentes foram montados no conjunto. Gatilhos podem ser disparados para enviar subconjuntos para a próxima célula de trabalho. Todo o histórico do subconjunto pode ser documentado garantindo uma rápida reação diante de problemas na linha.
A troca de informações e sinais é fundamental para a integração de uma gravadora à linha de produção. A Promarking oferece uma ampla gama de Interfaces, incluindo sinais de Start, Finish e E-Stop e envio e recebimento de Strings através das portas RS232 e Ethernet e dos protocolos Profinet, Profibus e OPC.
Montagem_ A necessidade de implementação de um código DPM (Direct Part Marking) ocorre principalmente em decorrência de ações de melhoria ligadas ao Seis Sigma, portarias regulatórias do Inmetro e em componentes de segurança do veículo tais como: motores e suas peças, cambio, eixos, suspensão, freios, rodas, rolamentos, ABS e Airbags.
Produtos com componentes incorretos que chegaram até a etapa final de controle de qualidade terão de ser retrabalhados fora de suas estações gerando custo extra e perdas de produtividade.
Gravar códigos nos componentes é o primeiro passo para cumprir normas regulatórias de segurança e atender expectativas do cliente final. Informação é indispensável! Ou você as grava desde o início ou não tem como voltar no tempo.
Montagem Final e Logística_ Operadores munidos de leitores podem identificar componentes da montagem final garantindo a seleção dos conjuntos e subconjuntos corretos. Este procedimento gera uma grande quantidade de dados para as operações subsequentes e reforça a rastreabilidade nos estágios finais da montagem.
Gravar e escanear o produto final para libera-lo para a próxima estação de trabalho. As informações podem incluir o nome do cliente, número do pedido ou ordem de produção e o local do destinatário de cada peça. A rastreabilidade é fundamental para questões de reparos, serviços e suporte ao cliente durante a vida útil do produto, além de garantir que um componente ou produto é autentico.
Rastreando componentes_ códigos de barras confiáveis são fundamentais para a manutenção de uma boa fluidez da linha de montagem. Não deixe que falhas de gravação se tornem gargalos na sua linha! As gravadoras a laser Promarking são capazes de gravar códigos permanentes e precisos durante toda a sua vida útil.
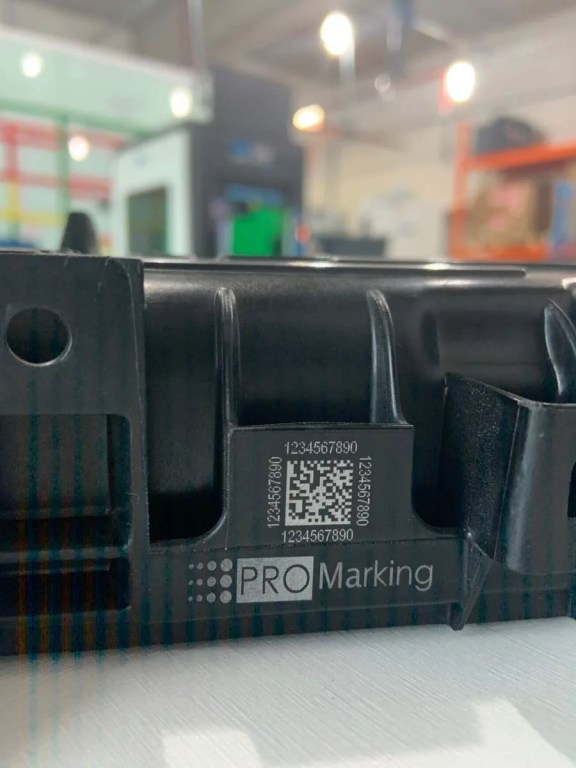
PASSO A PASSO DA RASTREABILIDADE AUTOMOBILISTICA
- Um virabrequim é gravado a laser com um código de barras contendo data e local de fabricação, linha de produção e nome do fabricante.
- Um leitor faz a leitura deste código na entrada da linha de produção de motores.
- O sistema da linha coleta e armazena diversas informações durante cada etapa da montagem, incluindo o código do virabrequim e suas tolerâncias dimensionais.
- Os leitores coletam os dados de códigos gravados em outros componentes como, por exemplo: bielas, pistões, cabeçote, válvulas e comandos agregando todos estes dados ao registro principal do motor.
- Estes dados são finalmente enviados e verificados pelo sistema ERP da empresa para assegurar a sequência correta de fabricação.
- Finalmente, um código de barras é gravado no bloco do motor e todos os dados são enviados para a montagem final linkando as informações do motor a um veículo especifico.
Um subconjunto do veículo está pronto e rastreado e assim, problemas podem ser facilmente identificados e tratados. Um código de barras gravado na superfície de cada componente garante um histórico completo e portanto, facilidade na resolução de qualquer problema.
gravação a laser